- Sustainability TOP
- Social
- Quality
Basic Approach
We gain the trust of our customers by providing products and services of high quality to our customers from various angles so as to be able to contribute to the solving of social issues toward the creation of a prosperous society.
Management Structure
Group-wide Quality Assurance System
Isuzu builds the QA system illustrated below with the aim of fully meeting its social and quality responsibilities as a manufacturer. Led by the Quality Assurance Division, all companies of the Isuzu Group work together to enhance our product quality. The Senior Division Executive of Quality Assurance Division chairs a monthly meeting of the Quality Assurance & Customer Satisfaction Improvement Committee (Quality Assurance & CS Committee), where the senior management of all divisions discuss and share information on quality-related facts and CS improvement so that the Committee can monitor how the divisions operate their quality management structures. The outcomes are shared to drive forward the quality assurance activities of the business divisions.
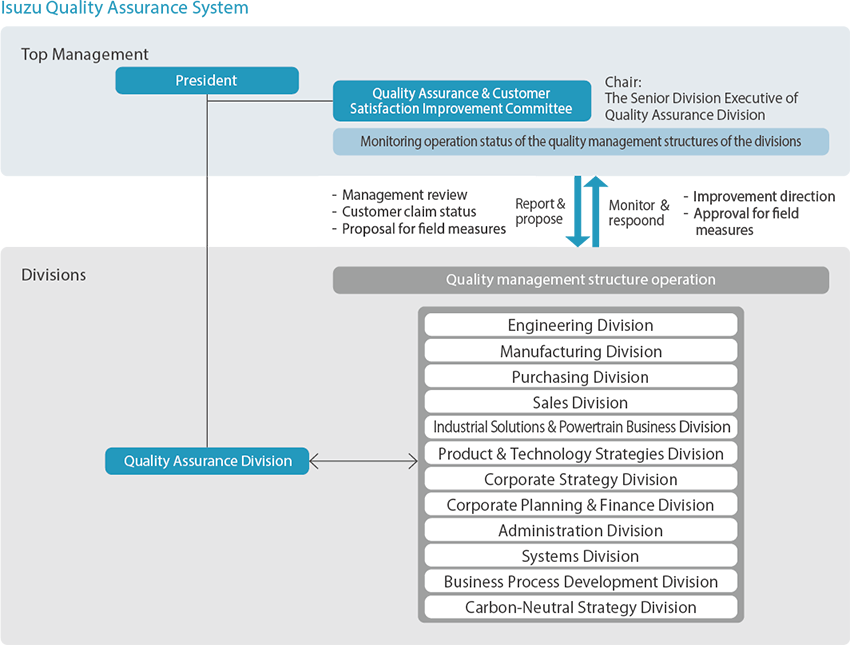
Improving Quality within Isuzu Group
By giving priority to quality in everything, Isuzu creates products that fully satisfy our customers and contribute to society, aiming to grow as a corporate group rich in humanity. To ensure the quality of Isuzu's products and services, it is important that we work carefully in each of the different stages of the value chain surrounding our products and services. We build readiness to assure quality in each of the different stages, including development, procurement, manufacturing and market launch, and manage the process accordingly. Through this, Isuzu ensures that its products and services fully satisfy customers. In the event that a customer has trouble with an Isuzu vehicle, we are organizationally ready to provide service and service parts to facilitate a quick recovery.
Isuzu always seeks to ensure that customers can feel secure about using Isuzu's products every day, and is committed to building long-term relationships of trust with customers.
Additionally, Isuzu's quality policy is to create and deliver products and services that satisfy its customers. Staying true to this policy, all companies in the Isuzu Group work together in quality improvement activities. This is based on our belief that we can deliver better products and services to our customers by improving the quality of business operations of all divisions, including back-office divisions. More specifically, we communicate our quality policy and share quality manuals throughout the Isuzu Group in an effort to improve the quality of our daily business operations.
Quality Management Structure (ISO 9001 and IATF 16949 certified)
All Isuzu business sites have earned ISO 9001:2015 certification, an international standard of quality management. Moreover, components to be delivered to General Motors Company have obtained IATF 16949:2016 certification, the standard for the automobile sector. Isuzu has been striving to enhance its operational quality using such measures.
Quality Activity Initiative Themes
The Isuzu Group has identified and is working on the following issues in an effort to promote business activities aimed at improving quality in all of its business areas.
- Product Quality Improvement
- Service Quality Improvement
- Operation Quality Improvement
Initiatives
Product Quality Improvement
Basic Approach behind Product Quality Improvement
Isuzu's mission represents our determination to go beyond our previous corporate philosophy. It emphasizes transport solutions for all goods and people, creating value that enriches society, while addressing pressing issues such as the need to attain carbon neutrality and adapt to a changing logistics landscape.
To achieve this, a number of activities have been undertaken to improve quality at every stage from product development and manufacturing to market operation.
Initiatives at the Development Stage
Our product development philosophy is to gain the trust of every person. This is supported by the basic concept of S.E.E. Technology, where S.E.E. stands for the three important issues of Safety, Economy, and the Environment. To acquire the high quality needed to underpin this philosophy, we set quality gates (milestones) at different stages in product development where the quality and the maturity of the products are confirmed so that product development can proceed. During the development stages below, Isuzu focuses on failures and preventing the recurrence of failures. Failure Mode and Effects Analysis (FMEA*) and other methods are used to enhance reliability and durability.
- *Failure Mode and Effects Analysis: This systematic analysis approach helps to discover potential failures and prevent failures and defects.
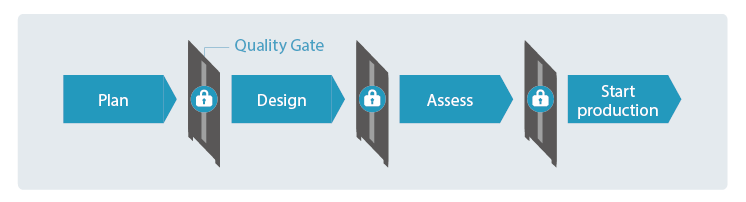
Safety Technologies
The quest for even higher safety in trucks—which have close ties to people and society—is a priority theme that does not change with the times. This is especially so for heavy- and medium-duty trucks, which have high total vehicle weights, as the damage caused is even larger. Therefore, the latest and most advanced responses are always required. In addition, trucks transport not only people, but also important goods. For example, even if an accident can be avoided by emergency braking when there is imminent danger, besides injury to people, there is still a high risk of causing damage to important goods such as when goods fall over. At Isuzu, we install necessary safety features to prevent accidents and reduce damage according to the vehicle type.
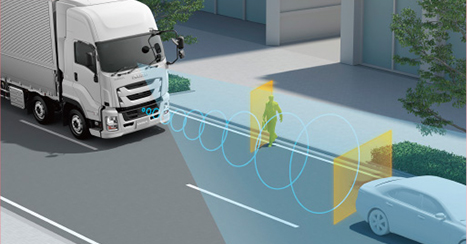
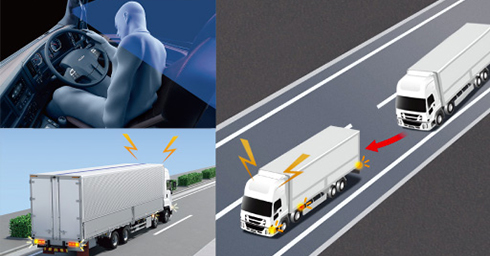
Initiatives at the Procurement Stage
Many of the parts and other items used in Isuzu's products are purchased from external business partners. When quality problems occur in purchased products, significant inconvenience is placed on customers using our products. While building relationships of trust with suppliers, Isuzu has established a quality management structure for products purchased from these suppliers to ensure a stable supply of good products to its plants. Going forward, we will continue to undertake quality improvement activities with our business partners and strive toward strengthening our supply chain.
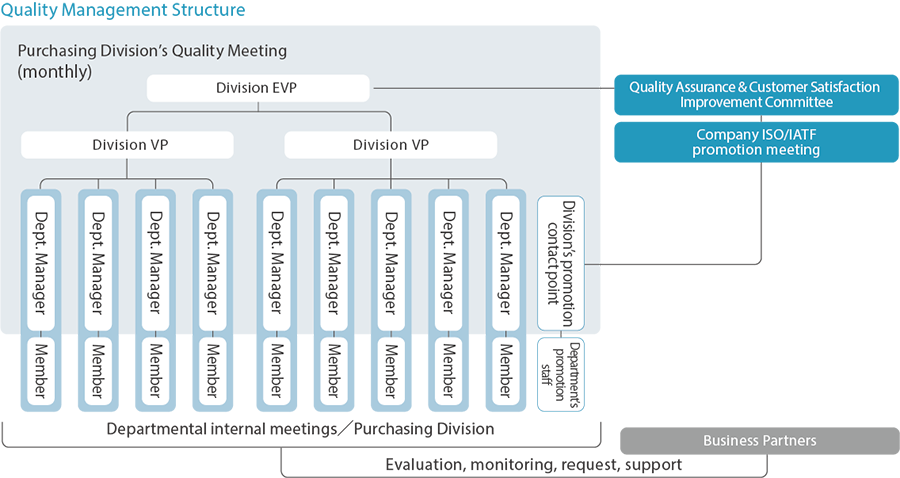
In Japan, we have a total of 680 business partners, about 90% of which are located in Japan. In terms of transaction amount, the procurement of vehicle and engine parts makes up about 80% of the total.
To monitor the delivery quality and market quality of our business partners, we calculate a monthly evaluation score based on factors such as the number of defect occurrences, the number of defects, and the severity of defects.
As a result, business partners whose delivery quality evaluation scores and defect counts do not meet certain standards are classified as companies to be managed, while business partners whose evaluation scores meet a certain level but have defect counts exceeding a specific limit and require improvement in delivery quality are classified as companies to be observed. We strive to improve delivery quality through initiatives such as monthly quality meetings. Due to these initiatives, approximately 91% of our business partners met the criteria for delivery quality evaluation in FY2024. While there were no companies classified as companies to be managed, there were several classified as companies to be observed. Improvement activities were conducted with these business partners to enhance quality.
Additionally, for some business partners, we conduct on-site audits during the direct supply contract renewal assessment, which occurs every three years, to verify the operation of their quality management systems. For new business partners, we conduct an on-site audit before beginning the business relationship to evaluate the effectiveness of their quality management systems and ensure they meet our criteria for trading.
We are also making progress with creating a BCP/BCM system and carrying out measures to reconfirm our supply chain and minimize the time it takes to restart operations in the event of an emergency. By improving the speed of our initial response and cooperating with our business partners, we are working to facilitate rapid recovery and creating a system that minimizes the impact on Isuzu product sales.
Initiatives at the Manufacturing Stage
Isuzu's customers require products of different specifications, and therefore Isuzu's products are available in many different variations. This is a characteristic of Isuzu. Isuzu is constantly committed to the development of human resources and improvement of production systems as it seeks to improve the quality of its diverse products to the same, high level and make them globally available.
Isuzu systematizes and integrates its quality-first concept, methods and manufacturing knowhow into ISUZU MONOZUKURI (IM). IM is a production method implemented in every Isuzu manufacturing plant in Japan and overseas countries. At heart, its concept is to ensure that Isuzu-badged vehicles can be manufactured based on a uniform concept of workmanship and quality control, in any plant around the world. To homogenize variation at a high level based on IM, production line managers gather each morning before starting work and have a quality audit meeting, through which we share information centering on quality and ensure that our production lines are always adaptable to changes.
Further, with IM-based efforts to deliver quality assurance on a global scale, Isuzu endeavors to become a company trusted by every customer who needs Isuzu's commercial vehicles and diesel engines. In addition to classroom and practical training on the fundamentals of IM, the employees involved in production are provided with applied practical training so they can apply the knowledge and skills acquired in basic training on the job site and make improvements according to the situation.
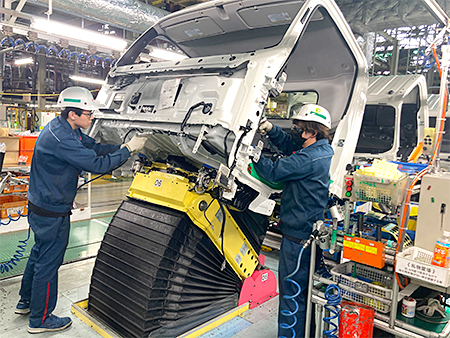
Number of Employees Who Received the Training in FY2024
There were 975 participants in FY2024, with an average activity rate of 21 hours per participant (2-5 days/person).
(Reference)
Core skills training: Group training on IM concepts and TPM* is provided.
Technical skills training: Approximately 30 types of practical skills training are delivered, including tightening training and engine assembly training.
- *TPM (Total Productive Maintenance) refers to the review and improvement of production equipment to streamline manufacturing.
Initiatives for Higher Field Quality
Isuzu strives to improve its field quality by paying close attention to customer opinions and analyzing and feeding them back to all quality-related processes to ensure that issues are addressed and improvements are made.
Initiatives toward Improved Field Quality
Taking advantage of the FQ management structure*, Isuzu collects quality information from markets then implements cause investigations and responds to issues promptly and accurately.
Isuzu Customer Center (Japan) gathers customer opinions, warranty repair records, and improvement requests from sales dealers as field quality information to direct to our quality improvements. The collected information is used in our efforts to comply with regulations from various countries including domestic safety regulations for road vehicles, and to respond to them even more quickly.
We also share information regarding the status of our response to field quality information and quality activities with top management and all employees on a monthly basis through our Quality Improvement Newsletter. Our Quality Improvement Newsletter features and shares quality activities such as the status of field quality improvement activities, the status of verification activities for initial quality of newly-launched vehicles in Japan, and the status of ISO/IATF activities. Through this, we seek to improve quality awareness throughout the entire Company.
- *FQ (Field Quality) management structure: An initiative to gather and distribute quality information from the markets for making improvements, based on the scheme illustrated below.
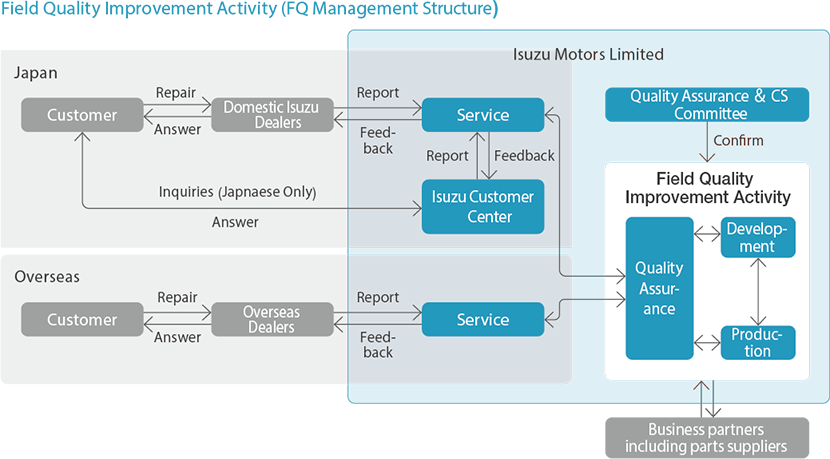
Initiatives for Recall Campaigns
The aim of the recall system is to prevent defective vehicles from causing accidents and to ensure the safety and assets of our customers and drivers. Based on an understanding of the aim and its philosophy, Isuzu conducts recalls as required by the Road Transport Vehicle Act, improvement measures, and service campaigns in an effort to ensure smooth operation of our customers' vehicles. We are always prepared to take prompt and appropriate actions from the customer's perspective, taking into consideration the diversification of users’ circumstances. Regarding complaints about safety-related defects, we conduct investigations and provide responses to 100% of the requests from authorities in each country.
- Recalls: Where a vehicle may not be able to meet safety regulations for road transport vehicles (regulations to ensure vehicle safety or prevent pollution) due to a problem in design or the manufacturing process, the vehicle may be repaired free of charge upon notification to the Ministry of Land, Infrastructure, Transport and Tourism. This is referred to as a recall.
- Improvement Measures: Where a vehicle cannot be left as is for safety reasons or for the prevention of pollution even though it complies with safety regulations, the system allows the vehicle to be repaired free of charge upon notification to the Ministry of Land, Infrastructure, Transport and Tourism, as long as the problem is attributable to design or the manufacturing process.
- Service Campaigns: A service campaign allows a vehicle to which neither recall nor improvement measures applies to be repaired free of charge upon notification to the Ministry of Land, Infrastructure, Transport and Tourism, for the purpose of improving its merchantability and quality.
Number of recalls and other notifications
FY2022 | FY2023 | FY2024 | |
---|---|---|---|
Recalls | 17 | 12 | 8 |
Improvement Measures | 2 | 0 | 0 |
Service Campaigns | 5 | 3 | 4 |
(Reference) UD Truck Recalls in FY2024: 5
Service Quality Improvement
Basic Approach behind Service Quality Improvement
Isuzu's mission represents our determination to go beyond our previous corporate philosophy. It emphasizes transport solutions for all goods and people, creating value that enriches society, while addressing pressing issues such as the need to attain carbon neutrality and adapt to a changing logistics landscape.
Consequently, it is important to ensure that our customers' vehicles keep working well and, if they don't, are quickly restored to working order. Isuzu provides standardized support both in Japan and overseas as part of its commitment to offering high-quality service. During the current COVID-19 pandemic, Isuzu's trucks have played an important role in supporting the availability of medical supplies and daily commodities. We are aware of Isuzu's mission and social responsibility to, in all circumstances, unfailingly deliver the vehicles customers need and help them to keep running satisfactorily by providing after-sales service without delay.
Thorough Service System
Isuzu is currently fully committed to post-delivery customer support.
Our customers always expect high-quality service. Isuzu pursues the establishment of high-quality, integrated service systems both domestically and internationally.
Japan
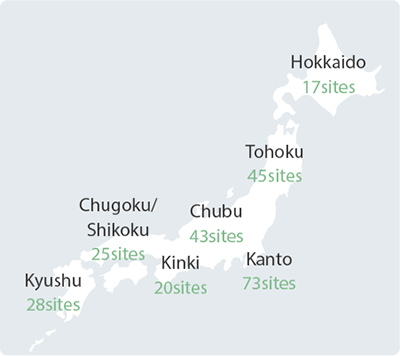
Overseas
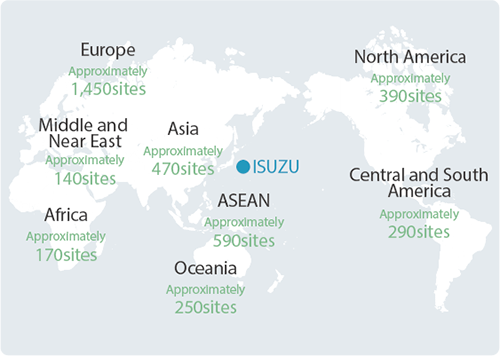
Parts Supply System
Isuzu delivers service parts in a timely and accurate manner to any place, leveraging its network of mother parts center (Tochigi, Japan) and regional parts centers in Japan and overseas. In addition, Isuzu Logistics Global Center commenced operations in April 2020. This is a state-of-the-art distribution warehouse designed to meet growing demand overseas for service parts. The new facility reinforces our readiness to supply parts to customers overseas. Moreover, the introduction of latest technologies has advanced the automation of in-warehouse work. Handling of heavy materials has been reduced in our in-warehouse work, which provides a better working environment for women and even elderly workers.
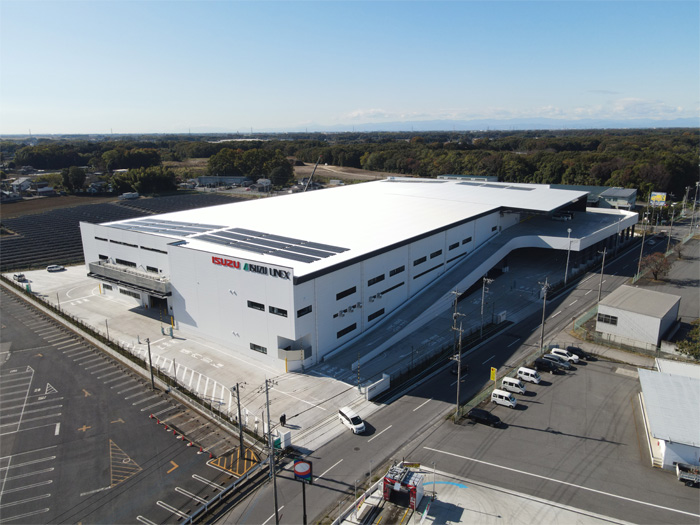
Japan
Seven regional parts centers ship the service parts to the service parts sites of Isuzu dealers.
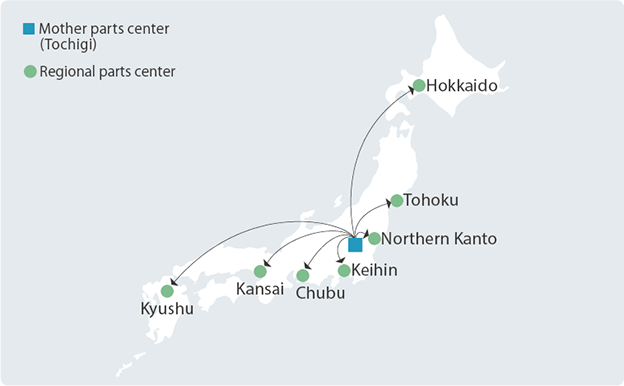
Overseas
Isuzu's extensive service parts supply network includes regional parts centers in the Middle and Near East, North Africa, North and Central America, Europe, and the ASEAN and Oceania regions.
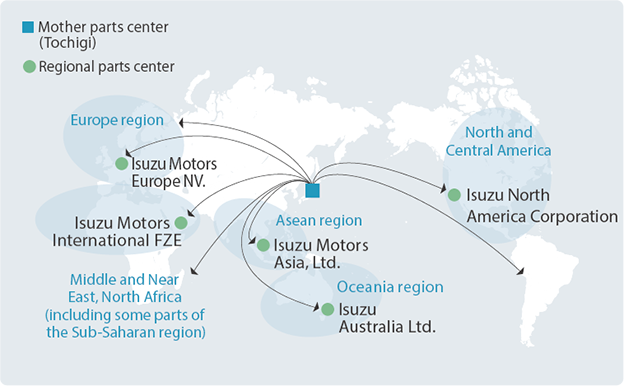
Improvement of Maintenance Engineering
Isuzu World Service Skills Competition (I-1GP)
The Isuzu World Service Skills Competition (I-1GP) gathers teams of servicing staff and engineers from different countries and regions across the world to compete in a skills and knowledge competition to find the world's best engineers. This is a global competition that aims to improve individuals' technical skills and the responsiveness of the engineers in Isuzu Group dealerships engineers (team technical skills). This international and interregional competition in skills and knowledge is aimed at improving service quality in their respective home fields so that Isuzu customers can enjoy the greatest satisfaction anytime, anywhere. The competition has been held since 2006.
From 2020 to 2022, due to the impact of the COVID-19 pandemic, the event was held online. However, in FY2024, the event returned to an in-person format for the first time in four years. Finalists who advanced from the preliminary rounds were invited to Japan and the event was held on November 1, 2023, at Pacifico Yokohama.
The contest included both individual and team competitions. In the team practical competition, teams consisting of two contestants and one coach performed vehicle inspection and fault diagnosis tasks using actual vehicles. Additionally, leveraging the competition system and content from the online service skills contest e-Competition conducted during the pandemic, both team/individual theoretical competitions and individual practical competition Virtual Fault Diagnosis were also held at the contest venue.
The competition featured 99 participants from 33 countries and regions, with a total attendance, including spectators, exceeding 1,000. Through I-1GP, we aim to promote the improvement of maintenance skills and the importance of technical training, and we will continue to work on enhancing service quality worldwide.
Results of the 18th I-1GP at CV division
- Group division: [1st] Japan, [2nd] USA, [3rd] New Zealand
Individual division: [1st] Japan, [2nd] Japan, [3rd] New Zealand
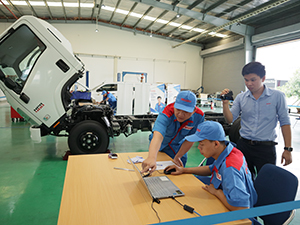
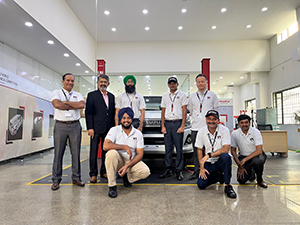
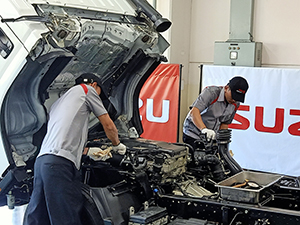
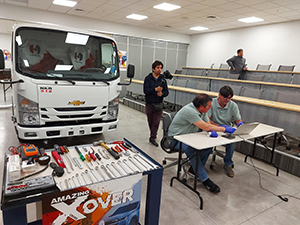
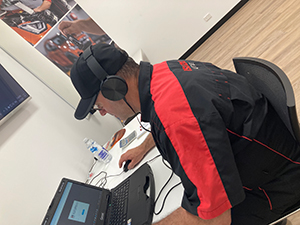
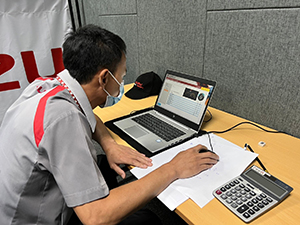
National Service/Parts Skill Competition
Isuzu holds an annual competition for workers to compete in the skills they have accumulated through their everyday work. The purpose of this contest is to improve the skills of Isuzu's after-sales staff, promote education, enhance customer satisfaction, and boost the morale and solidarity of Isuzu after-sales staff.
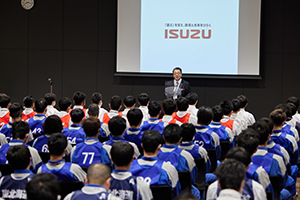
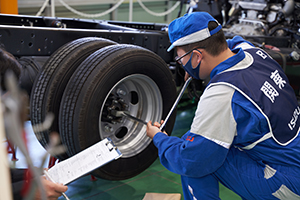
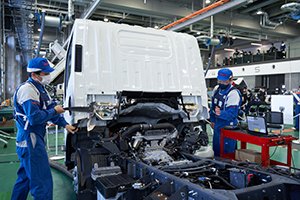
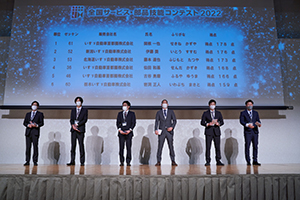
Training Employees of Isuzu Dealers
We offer training programs to the service staff and engineers that support the transport needs of our customers so they can brush up on their service operations and maintenance engineering skills and learn more advanced repair techniques.
In addition to conventional group training at the Isuzu Monozukuri Service Training Center, we are further enhancing the skills of our workforce by introducing remote training (using web conferencing systems and e-learning platforms) and adapting self-hosted training to be held at dealerships.
FY2024 Results
Number of Courses | Number of participants | Training Method | ||
---|---|---|---|---|
For service engineers | 29 courses | 45 sessions | 642 | Group Training |
0 course | 0 session | 0 | Remote Training | |
7 courses | 40 sessions | 455 | In-house Hosting | |
For service advisors | 6 courses | 8 sessions | 114 | Group Training |
14 courses | 26 sessions | 283 | Remote Training | |
0 course | 0 session | 0 | In-house Hosting |
Feedback from participants
- I was able to learn about the internal structure of parts that cannot be understood from regular maintenance work, and it was very educational. In the future, I hope to make use of this knowledge in training junior staff. (Service Engineer, Dealerships)
- The in-depth explanation of the usage of the diagnostic tool was helpful in advancing my practical skills. (Service Engineer, Dealerships)
- After receiving this training, the areas I was not confident in have now turned into strengths. I will apply what I have learned in the field going forward. (Service Engineer, Dealerships)
Maintenance Engineering Workshop in FY2024
30 sessions
Customer Support
Various Support Programs, including Fuel Efficiency and Safe Driving Seminars
Isuzu has been offering its customers seminars on fuel-efficient and safe driving since 1995. In recent years, we have been conducting demonstrations of key points for the use of vehicle devices and accident prevention, workshops on legal and regulatory trends and many other seminars based on customers' needs. Within Japan, these seminars are conducted at seminar facilities named Isuzu Premium Clubs located on the premises of our Fujisawa Plant and Isuzu Hokkaido Proving Ground. The Clubs are equipped with test courses and are exclusive for our customers. Seminars are also conducted at dealers all over Japan. To date, we have held these seminars overseas for customers from 31 countries. We strive to help our customers in Japan and all over the world to use our vehicles in safer and more eco-friendly ways.
Isuzu Customer Information
The Customer Information section of the Isuzu website draws the attention of users of Isuzu vehicles to potential incidents or failure risks arising from misuse or other problems.
Long Periods of Use
In recent years, along with changes in economic circumstances and other factors, our customers have tended to use their vehicles for longer periods and their mileage has been increasing. The safety of vehicles that have been in use for a long time can be guaranteed by ensuring that regular inspections and maintenance are performed. Isuzu keeps a sufficient stock of periodic replacement parts on hand to prevent failures from occurring and to meet customers' needs for periodic maintenance. We will keep working on inspection and maintenance, also taking into consideration the way in which vehicles are used and their use over extended periods.
Isuzu Customer Center
Isuzu Customer Center (Japan) was established for the purpose of applying customer feedback to product quality improvement. Customer feedback is shared with relevant departments both internally and externally to improve the quality of our products and services. We also provide opportunities to listen to the voices of our customers through internal training programs to enhance our customer-first approach and our sensitivity to what our customers want.
Customer Testimonials
We received very encouraging news from a transportation company customer. The FORWARD, one of our medium-duty trucks, is about to reach a mileage of 1.3 million kilometers with no major breakdowns. When this news was shared by the Isuzu Customer Center with the sales company, the sales company decided to present a letter of appreciation to the customer.
The customer expressed gratitude for the letter of appreciation and praised the branch manager and the sales representative, who had visited multiple times and provided kind support. Additionally, we heard that the customer has displayed the letter of appreciation at their office entrance, and it has received very positive feedback from visitors.
According to information from the branch manager, the customer is very meticulous about vehicle maintenance, promptly taking the vehicle for inspection if there are any signs of issues.
We believe that the customer's careful maintenance of their vehicle, along with the long-term support from our sales company, has contributed to achieving such a remarkable result.
Moving forward, the entire Isuzu Group will continue to focus on providing products that emphasize reliability and durability, as well as delivering high-quality after-sales service, to support our customers' businesses.
Actual Incoming Calls to the Isuzu Customer Center in FY2024
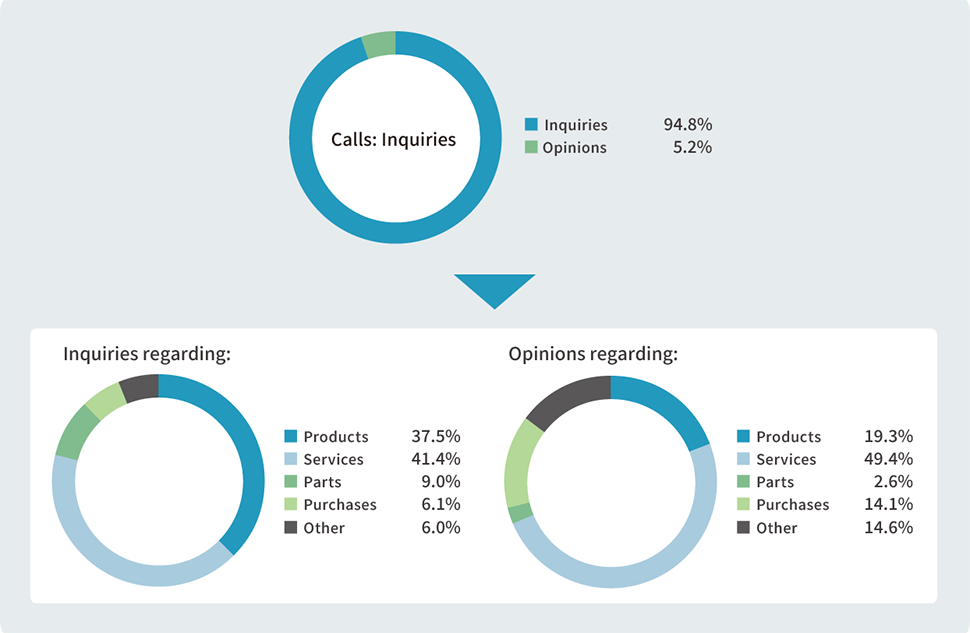
Intangible Support
MIMAMORI (Telematics for Commercial Vehicles)
Isuzu has also been dedicated to supporting the software side of commercial vehicles. A symbol of this effort is the telematics system for commercial vehicles known as MIMAMORI. It reads data from the vehicle's onboard control computer and connects via information communication to support fleet management and dynamic monitoring. MIMAMORI offers a range of services, including support for daily legal compliance such as driving reports, digital tachographs, and labor management; advanced dynamic monitoring functions for tracking the vehicle's current location and condition; eco-driving support; safety driving encouragement; and driver training. This comprehensive service package significantly contributes to the efficiency of fleet management for our customers.
PREISM (Advanced Genuine Maintenance Service Utilizing Vehicle Data)
PREISM, an advanced genuine maintenance service, provides predictive and preventive maintenance at Isuzu service centers before a malfunction occurs, based on condition data transmitted from vehicles. This helps to shorten the vehicles' downtime and maintain their operation.
- Prevention:
Servicing details and maintenance cycles differ depending on the status of use of the vehicle. However, PREISM tracks data on each vehicle's condition, thus enabling optimally predictive and preventive maintenance for each vehicle, which checks malfunctions. - Immediate repairs:
Even if a malfunction occurs, our Isuzu service centers can estimate servicing details from the malfunction data obtained prior to warehousing. Thus the vehicle's servicing time can be shortened. This can also reduce downtime and makes the vehicle's operation more secure.
The full lineup of the heavy-duty GIGA, medium-duty FORWARD, and light-duty ELF trucks comes with a data transmission terminal as a standard feature, providing PREISM to support stable operation of a customer's vehicle.
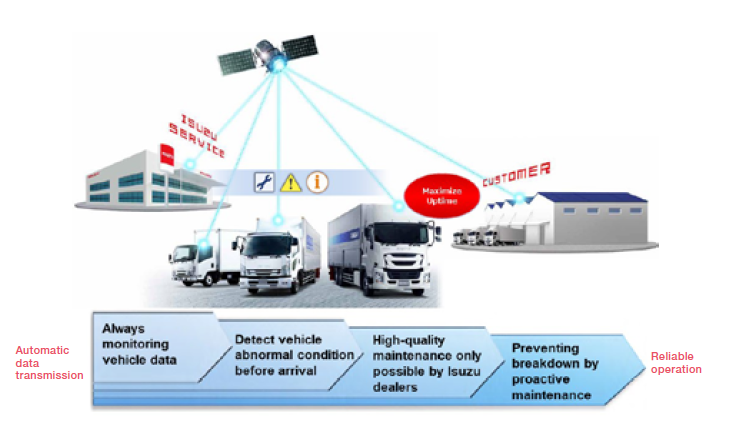
EVision
Alongside the launch of Isuzu's first mass production battery electric vehicle (BEV), the 'ELF (N-Series) EV,' Isuzu has developed the total solution program 'EVision*1' to support customers considering introducing commercial BEVs and has begun service provision. The support provided in EVision includes finding solutions to EV introduction issues, quantifying the CO2 emission reduction benefits, and proposing further decarbonization initiatives to move toward to carbon neutrality.
- *1'EVision' combines the 'EV' of electric vehicles with 'Vision' in its many senses including sight, foresight, and future aspirations. It expresses Isuzu's support and initiatives for transparency regarding the issues and operations involved in EV introduction and its determination to provide solutions, thereby showing customers the way toward achieving carbon neutrality.
Operational Quality Improvement
Basic Approach behind Operational Quality Improvement
Isuzu's mission represents our determination to go beyond our previous corporate philosophy. It emphasizes transport solutions for all goods and people, creating value that enriches society, while addressing pressing issues such as the need to attain carbon neutrality and adapt to a changing logistics landscape.
The quality of our products and services is derived from the work quality of each and every employee. Isuzu leverages efforts to raise awareness about quality and knowledge since we believe that enhancing the performance quality of each individual employee—and not just those divisions directly involved in product quality—creates the quality that meets customer needs.
Education for Raising Awareness and Knowledge among Employees
The foundation of work is the experience, knowledge (tools and methods), and skills possessed by each individual. But even with experience, knowledge and skills, it does not necessarily follow that the work will be done with good quality. For employees to maximize their skills and improve the quality of their work, it is essential that they remain motivated to do a good job. Isuzu therefore strives to improve the quality of its operations by educating employees to raise awareness and knowledge acquisition.
Discussions among Employees
To raise awareness about operational quality, Isuzu is holding a series of discussions for employees to talk about doing a good job from the customer's perspective, using customers' telephone inquiries received by the Isuzu Customer Center and the annual Quality Month* Message which is delivered from senior management to employees in November every year.
During Quality Month, the focus is on each individual reflecting on what constitutes good work, gaining insights and clues on how to achieve it, and taking concrete actions based on those insights.
- *Quality Month: The Union of Japanese Scientists and Engineers, the Japanese Standards Association, and the Japan Chamber of Commerce and Industry have designated every November as Quality Month for the promotion of quality improvement activities.
Message for Quality Month FY2024
Theme: Let's reflect on our work and verbalize it to find clues for delivering good work!
Target period: November to February
Target: All employees
Results: 8,654 employees participated
Reason for theme selection:
In an era where the environment surrounding Isuzu is becoming increasingly intense, what is now required of us to achieve our goal of becoming an innovation leader that advances the world through reliability × innovation is to further enhance reliability while fostering innovation. To do this, we should intentionally verbalize our work, making it easier to identify our true thoughts and uncover any unrecognized issues. This process will ultimately lead to improved work quality.
Quality Awareness Education for Isuzu Dealers
To raise the quality awareness of all Isuzu Group employees, quality awareness training is provided to dealers across Japan to reinforce the importance of quality-related tasks such as the accurate and prompt provision of information, reliable recall of defective parts, and early implementation of recall repairs.
Number of Locations Where Training Was Held in FY2024
22 places
Improving Knowledge (Knowledge-enhancing Program)
As a quality-related knowledge education program for employees, we conduct legal education, focusing on the Road Transport Vehicle Act/Recall System. The aim is to ensure that our employees understand the laws related to the quality of Isuzu products. Additionally, we offer a course for developing experts skilled in the statistical analysis necessary for solving problems. The courses are aimed for employees to acquire problem-solving skills and practical skills for effectively encouraging quality improvement in the workplace.
Results
Road Transport Vehicle Act/Recall System: 157 participants
QC Seminar Basic Course*: 22 participants
- *Conducted by the Union of Japanese Scientists and Engineers
Isuzu Technical High School
Isuzu Technical High School provides education and training programs for our new technical employees (trainees) who are high school graduates. There are two courses: a three-month training early selection course and a training course. Both courses emphasize the necessary for Isuzu's monozukuri knowledge, skills, and attitude required as Isuzu technical employees. The trainees who show very high aspirations in manufacturing (monozukuri) enter the National Skills Competition to learn about the results of their day-to-day technical training and further improve their skills.
Moreover, school instructors to guide the trainees are selected from our employees working in the field. This allows the instructors to review their own operational knowledge, and at the same time to learn how to develop talent. As a consequence, the instructors will also improve.
In addition to developing trainees into full-fledged workers, the engineers involved with the training process should hone and hand down their skills. This should then contribute to qualitatively improving Isuzu's products.
Competition Results
The 61st National Skills Competition, November 17-21, 2023, Aichi International Exhibition Center
Machine Assembly: 1 Honorable Mention
Automobile Sheet Metal Work: 1 Silver Prize
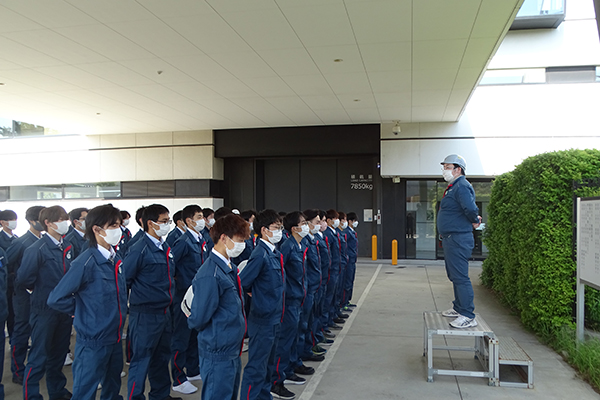
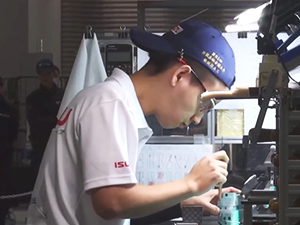
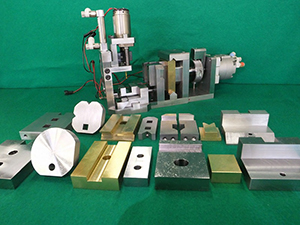
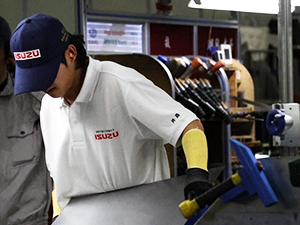
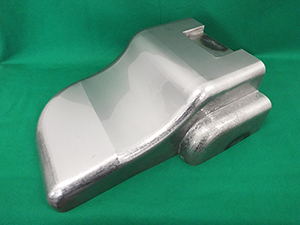