- Sustainability TOP
- Social
- Supply Chain Management
Basic Approach
We will share and collaborate with our business partners on our PURPOSE, 'Moving the World - for You,' as outlined in the ISUZU ID, and work together in purchasing activities. We conduct open and fair transactions and maintain mutual communication with the various business partners involved in our supply chain to build relationships based on trust.
Basic Approach to Procurement Activities
Isuzu recognizes that gaining the cooperation and trust of its stakeholders, including its business partners, in the areas of Isuzu's activity such as the environment, quality, compliance, human rights, and community/social contributions, is extremely important to earning the trust of society, contributing to the sustainable development of society, and fulfilling its corporate social responsibility. To this end, it is working to address a variety of issues.
Isuzu established the Purchasing Basic Vision and Purchasing Basic Policy in 1997 to illustrate the direction of its procurement activities and maintain consistency across these activities. Our Purchasing Basic Vision and Purchasing Basic Policy are thoroughly communicated to new recruits and, through introductory training, to transferees from outside the Purchasing Division.
Many of the parts and other items used in Isuzu's products are purchased from external business partners.
The occurrence of a quality problem with purchased items or the manifestation of environmental, social, or business continuity risks affecting the supply may cause significant inconvenience to customers using our products. To prevent such situations, Isuzu is strengthening its monitoring system regarding quality management, as well as environmental, social, and business continuity measures. Going forward, Isuzu will continue its purchasing activities based on mutual trust with its business partners and will aim to establish a more resilient supply chain to ensure the stable procurement of quality products.
Purchasing Basic Vision
Isuzu ensures satisfactory quality, delivery and quantity of purchased parts so that smooth production is achieved through our purchasing activity. We also help to support the spread of new technologies through our purchasing activity in the market, and we strive to ensure our purchasing activity contributes the profitability of the company. Our Purchasing Division ensures satisfactory quality, delivery and quantity of purchased parts.
(Established: July 1997, last revised: April 2008)
Purchasing Basic Policy
- With “quality” as the first priority, Isuzu seeks to create and offer products that would satisfy our customers.
- Isuzu aims to procure domestic or overseas parts, under fair competition, if the parts are satisfactory in terms of quality, pricing and delivery.
- Isuzu enhances corporate competitiveness while developing procurement schemes aiming to form win-win relationships with our business partners. Isuzu supports the objectives of the Declaration of Partnership Building, which aims to enhance the added value across the entire supply chain and establish a sustainable and mutually beneficial relationship with business partners. Isuzu has publicly announced its own the Declaration of Partnership Building.
Thorough Enforcement of the Purchasing Basic Vision and Purchasing Basic Policy among Purchasing Division Members
Our Purchasing Basic Vision and Purchasing Basic Policy are written in the Purchasing Division Compliance Guidebook which is available on our in-house database for viewing by members of the Purchasing Division at any time.
Explanation about our Purchasing Basic Vision and Purchasing Basic Policy was added to the introductory training for transferees to the Purchasing Division in FY2024. In this way, all employees of the division are thoroughly educated on the Basic Vision and Policy.
In addition, a seminar on the Act Against Delay in Payment of Subcontract Proceeds, etc., to Subcontractors and the Guidelines for Appropriate Trade in the Automobile Industry is held in an effort to encourage understanding about and compliance with the Act and the Guidelines which members of the Purchasing Division must know well.
Management Structure
Isuzu holds a Purchasing Division's Quality Meeting once a month for reporting and discussion on topics such as the quality of the previous month's purchased parts, results of audits on new business partners and results of internal audits and external assessments related to ISO and IATF. The Purchasing Division holds a Quality and Compliance Promotion Meeting and an Environmental Meeting once a month each. Information from these committees is passed to all departments within the Purchasing Division. The Purchasing Division's policy on activities related to compliance and the environment is determined at these meetings.
Implementation of Departmental Education
New employees and other employees newly assigned to the Purchasing Division receive introductory training on compliance and sustainability. All division members are provided with seminars on the Act against Delay in Payment of Subcontract Proceeds, etc. to Subcontractors. Furthermore, we conduct an seminars on EV batteries and FCVs as part of our organization's efforts to deepen knowledge about zero-emission vehicles and work toward achieving a decarbonized society.
Business Partner Consultation Service
We maintain a Business Partner Consultation Service as part of our Risk Management Dept. Compliance Management Group. It offers impartial consultations to our business partners. We are available for consultation with business partners regarding compliance issues.
Initiatives
Isuzu Supply Chain
Isuzu chooses its Business Partners according to a fair and equitable selection process regardless of whether they are based in Japan or overseas. Starting in 2023, we have incorporated sustainability assessments into our business partner selection process. We are engaged in purchasing activities aimed at mutual prosperity with our business partners and are implementing similar initiatives at our global procurement bases to strengthen Isuzu's competitiveness. Isuzu in Japan have a total of 675 domestic and overseas business partners. About 90% of these partners are based in Japan. In terms of transaction amount, the procurement of vehicle and engine parts makes up about 80% of the total.
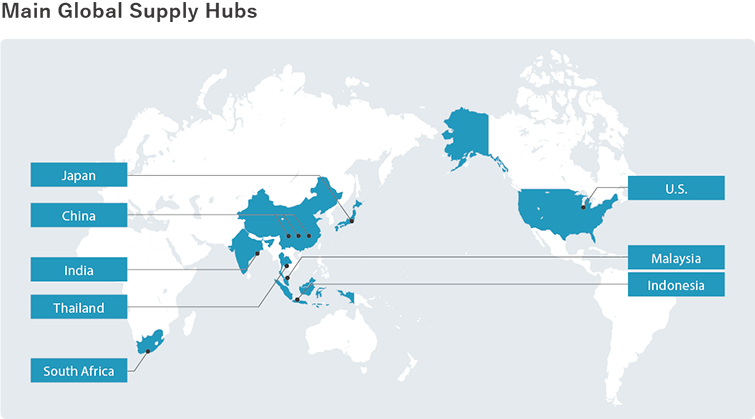
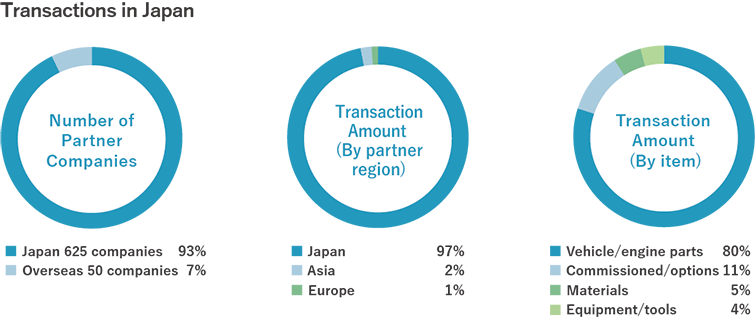
Regional Development and Job Creation
In the countries and regions where Isuzu operates, Isuzu promotes the use of local parts to contribute to the development of the local automotive industry and employment.
Various Guidelines for Business Partners
Isuzu Group Supplier Sustainability Guidelines
Until recently, Isuzu has been conducting socially responsible procurement activities in collaboration with our business partners based on the Supplier CSR Guidelines. However, considering the changing trends in sustainability and the expectations of our stakeholders, in December 2022, we revised and updated the guidelines to create the Isuzu Supplier Sustainability Guidelines (hereinafter the Guidelines). In April 2024, the guidelines were retitled as the Isuzu Group Supplier Sustainability Guidelines, and efforts to expand their implementation to all Isuzu Group business partners are underway.
The guidelines reference various Isuzu Group policies, including the Isuzu Group Human Rights Policy, the Isuzu Group Responsible Minerals Sourcing Policy, and other relevant Isuzu Group policies, as well as internationally recognized standards and frameworks. In the request items for business partners, the guidelines aim to enhance the content to share values related to sustainability, such as environmental and human rights issues, across the entire Isuzu Group supply chain. We encourage business partners to utilize these guidelines to advance their own initiatives and to actively promote and understand these practices not only within their own operations but also throughout their supply chain.
We kindly request our business partners to agree with Isuzu's principles and confirm their commitment to comply with the requirements of the Guideline for all products and services supplied to Isuzu, by signing an agreement. As of May 2024, we have received signatures from business partners representing approximately 95% of our annual purchasing amount.
Additionally, we created a Self-Assessment Questionnaire (SAQ) to evaluate whether our business partners are adhering to the initiatives outlined in the Sustainability Guidelines, and we began conducting surveys using this SAQ in FY2024. In FY2024, we requested submissions of the SAQ from 284 key business partners (accounting for 96% of our annual procurement spend). As a result, sustainability-related risks were identified at 17 of these companies. For those business partners where risks were identified, we have conducted on-site or remote interviews and are working with them to implement improvements.
Isuzu Green Procurement Guideline
The Isuzu Group has established the Isuzu Green Procurement Guidelines, which introduce our Charter on the Global Environment and summarize the environment-related requests we have for our business partners by type of industry. (Last revised: October 2020.) Through the Isuzu Green Procurement Guidelines, we obtain an understanding of Isuzu's environmental initiatives from our business partners, and at the same time request that they promote environmental activities.
Communication with Business Partners
Isuzu is strengthening communication with its business partners through briefings and meetings. In FY2024, while making use of web tools as needed, we have gradually increased face-to-face communication in response to the changes in the situation following the COVID-19 pandemic. Also, we try to remain respectful in communicating with our business partners. We are enhancing two-way communication with our business partners based on mutual trust, offering support by inquiring if they have any concerns or difficulties. We are confident that this kind of communication will contribute to strengthening the supply chain.
Main Opportunities for Communication with Business Partners
- New Year's business leaders' forums
- Procurement policy briefings
- Production briefings
- Quality policy briefings
- Isuzu Kyowakai*
- *Isuzu Kyowakai: A cooperative association comprising Isuzu's business partners
Deployment of Isuzu Group Supplier Sustainability Guidelines and ISUZU Green Procurement Guidelines
The failure of a business partner to fulfill its corporate social responsibilities would significantly and adversely affect Isuzu's reputation and its production activities. For example, the occurrence of misconduct—such as falsification of inspection data or human rights-related problems—from our business partner would adversely affect Isuzu's image and, through actions such as discontinuation of supply of purchased parts, Isuzu's production activities. This would inconvenience the customers who use Isuzu's products. To avoid such risks, we ask our business partners to follow our Sustainability guidelines. When contracting with new business partners, we request that they follow the Isuzu Group Supplier Sustainability Guidelines, which include human rights, the environment, and anti-corruption measures such as restrictions on unfair business dealings and prohibitions on offering entertainment, gifts, and money.
Additionally, through the ISUZU Green Procurement Guideline, we ask our business partners to learn about Isuzu's environmental initiatives and promote environmental activities.
The guidelines are posted on the Isuzu Supplier Portal Site and the Isuzu website to inform business partners. We request our business partners to agree with Isuzu's approach and sign a consent form to confirm their compliance with the requirements of these guidelines for all products and services supplied to Isuzu.
Monitoring the Efforts of Our Business Partners
Quality
To monitor the delivery quality and market quality of our business partners, we calculate a monthly evaluation score based on factors such as the number of defect occurrences, the number of defects, and the severity of defects. As a result, business partners whose evaluation scores and defect counts do not meet a certain standard are selected to be companies subject to management, and business partners whose evaluation scores meet a certain threshold but have defect counts exceeding a specific limit are selected as companies subject to observation, indicating a need for improvement in delivery quality. We strive to improve delivery quality through efforts such as holding monthly quality meetings. In FY2024, the quality of the deliveries improved and approximately 91% of our business partners attained the standard score of delivery quality evaluation. None of the business partners was determined to be a company subject to management by failing to attain a certain standard of quality evaluation. However, some fell within the definition of a company subject to observation. We joined these business partners in their improvement activities and encouraged them to strive for better quality.
In addition, we conduct an on-site audit of certain business partners when they undergo a triennial assessment for the renewal of a direct supply contract, to keep updated on their quality management structure operations. We conduct an on-site audit of our new business partners before starting business relationships with them and evaluate the effectiveness of their quality management structures to see if they meet requirements for trading with us.
BCP
From the perspective of business continuity, numerous challenges need to be addressed regarding our future production activities both in the short and medium-to-long term. These challenges include shortages in parts supply, infectious diseases, production plan changes due to natural disasters, and operational adjustments, among others. Furthermore, it is essential to be mindful of geopolitical risks. In FY2024, due to the emergence of procurement risks such as import restrictions on raw materials and the need to reroute shipping lanes because of conflicts, we have considered holding larger inventories and explored the possibility of sourcing from regions not affected by such risks.
We are also promoting the establishment of a BCP/BCM system to verify the supply chain and will tackle the new challenge of visualizing the supply chain. In the event of a natural disaster, we utilize our system to promptly request that business partners responsible for reporting the extent of the delivery impacts they are facing. Since FY2024, we have introduced a new system to collect information on the supply chain. The supply chain is constantly evolving, and new challenges arise daily. Therefore, we continuously update the information we collect and promote activities aimed at improving overall standards. Through these activities, we aim to identify vulnerabilities within the supply chain, pursue strategic inventory management, reduce lead times, and eliminate geopolitical risks. Additionally, we are establishing a system that accelerates initial responses during disasters, working in cooperation with our business partners to ensure early recovery efforts and minimize the impact on Isuzu product sales.
Environment
Isuzu requests that its business partners report their activities related to the promotion of environmental management structures through the Voluntary Assessment Report on Environmental Management. We asked 367 business partners to conduct voluntary assessments for the Voluntary Assessment Report on Environmental Management for FY2024. The evaluation results showed a record-high response rate of 98.6%, surpassing last year's results, and the highest average score to date. We confirmed that the number of business partners engaged in environmental activities is increasing. Improvements were observed in the increased number of initiatives related to CO2 reduction activities in logistics, as well as in energy-saving activities, water consumption reduction, and waste reduction activities. This confirms that the awareness of environmental activities among our business partners has further increased. Additionally, we have joined to the CDP Supply Chain Program from FY2023 to promote efforts related to climate change and to track our business partners' GHG emissions. We received responses from 190 business partners, representing approximately 90% of our annual purchases, from those we requested to participate. Starting from FY2024, we have introduced an award for our business partners' environmental initiatives called the Sustainability Award (Environmental). Isuzu recognizes that promoting environmental activities is vital to strengthening its supply chain and will continue to work towards the gradual reduction of GHG emissions.
Main voluntary environmental assessment items
- Environmental management structures
- Notification of environmental personnel
- Compliance with environment-related laws and regulations
- Promotion of energy-saving activities
- Reduction of water consumption
- Reduction and appropriate treatment of waste
- Reduction of emissions of regulated chemical substances
- Submission of voluntary environmental management structure evaluation report
- Managing environmentally hazardous substances
- Reduction of CO2 emissions and packaging/shipping materials in logistics
Human Rights
Since FY2022, we have been conducting surveys on our business partners' efforts regarding responsible mineral procurement and human rights, as part of our sustainability initiatives. Starting from FY2024, we have begun conducting surveys using a new Self-Assessment Questionnaire (SAQ) aligned with the content of the Isuzu Supplier Sustainability Guidelines. In FY2024, we requested submissions of the SAQ from 284 key business partners (accounting for 96% of our annual procurement spend). As a result, sustainability-related risks were identified at 17 of these companies. For those business partners where risks were identified, we have conducted on-site or remote interviews and are working with them to improve.
Approach to Surveying Sustainability Initiatives

Cybersecurity
Since FY2022, we have been reviewing the JAMA/JAPIA cybersecurity guidelines of our business partners to confirm and improve their cybersecurity measures. We kindly request that our business partners conduct a self-check using the Automotive Industry Security Check Sheet. Moreover, starting in FY2023, we have conducted cybersecurity management system establishment and operational status checks for business partners handling products subject to UN-R155 and domestic regulations (Road Transport Vehicle Law Safety Standards) to ensure they comply with vehicle product cybersecurity requirements. (28 companies in FY2023, 15 companies in FY2024 / Total of 43 companies)
In the future, we will continue to promote comprehensive cybersecurity measures among our business partners. To achieve this, we will conduct regular surveys to assess their improvement status and provide appropriate support from Isuzu as needed. Furthermore, to ensure compliance with regulations, we will conduct checks on the vehicle product cybersecurity management systems of the relevant business partners.
Environmental Activity Seminars
In FY2024, we informed our business partners about environmental activity plans, chemical substance regulations, and Isuzu's policies through the production briefings. Each briefing was held twice a year, with approximately 500 participants at each session. Additionally, adapting to the changing circumstances post-pandemic, we conducted visit activities and environmental seminars for our business partners. We collaborated with a total of 6 companies during these visits to review and discuss their environmental initiatives. At the environmental seminars, we had presentations by instructors from the Energy Conservation Center. Approximately 400 participants attended, where we mainly introduced energy-saving case studies and explained related concepts, aiming to enhance the overall level of our supply chain. In FY2025, we will continue our efforts to upgrade the entire supply chain.
Human Rights Seminars
To promote human rights due diligence initiatives in our business partners' supply chains, we continued our efforts in FY2024 by hosting an online seminar titled Responsible Mineral Sourcing Seminar. This seminar, featuring external experts, focused on the environment surrounding mineral sourcing and the due diligence expected from companies regarding minerals.
In FY2025, we will raise the level of our efforts and further promote understanding of human rights issues among our business partners.
Responsible Mineral and Raw Material Sourcing
Isuzu considers the use of conflict minerals to be a serious problem in the supply chain as these minerals cause human rights infringements, environmental destruction, and illegal mining in conflict zones, and are used to finance militant forces. Therefore, we request confirmation of non-involvement in conflicts upstream in the supply chain through the Isuzu Group Supplier Sustainability Guidelines. In FY2022, we launched a survey on the use of conflict minerals in our business partners' supply chains and the status of their initiatives for responsible mineral sourcing. Since FY2023, we have been conducting surveys using the CMRT and EMRT, which are standardized formats provided by Responsible Minerals Initiative* (RMI). In FY2024, we established the Isuzu Group Responsible Mineral Sourcing Policy. We will continue to ask our business partners to promote responsible mineral sourcing.
- *Responsible Minerals Initiative: An organization based in the United States that addresses conflict minerals issues
[Isuzu Group Responsible Mineral Sourcing Policy]
Interview with Technical Intern Trainees
At Isuzu, we are addressing issues related to foreign workers, including overseas technical intern trainees, as a significant human rights issue since FY2023. In FY2024, we conducted interviews with overseas technical intern trainees at two companies, including a Group company and a business partner, with the assistance of a third-party organization (Caux Round Table Japan).