CO2排出量削減 - CO2排出量生産高原単位推移
目標
CO2排出量生産高原単位:2015年度までに2010年度比5%以上削減
2014年度実績
CO2排出量:185千トン
CO2排出量生産高原単位:21.8 トン/億円(2010年度比8%減)
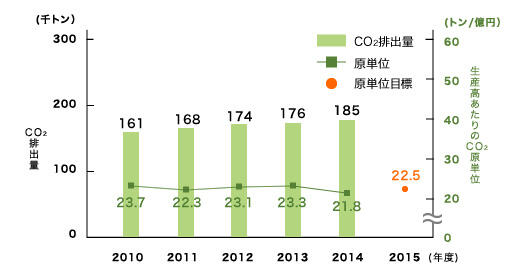
生産量の増加によりCO2排出量は2013年度比増加しましたが、継続したCO2削減対策の実施により、生産高原単位は目標通り削減できています。
今後はエネルギーのJIT(ジャストインタイム)化の推進などを行い、目標値達成に向けて更なる活動を進めて行きます。
CO2削減のための主な取り組み
- 工場の電力と熱源供給のための大規模コージェネレーションの活用
- 新規建物用の小規模コージェネレーションの活用
- 多管式高効率ボイラーの活用
- 空調設備や各種動力設備のインバーター化
- エコストップ・アイドリングストップ活動の推進
- 大型エアコンプレッサーの運転効率向上(小型機配備)
- 再生可能エネルギーを利用した照明の導入
- 高効率照明器具の導入
- コージェネレーションシステム(8,730kW)の追加(栃木工場)
- 事務所太陽光発電設備(220kw)の設置(藤沢工場)
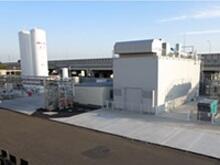
栃木工場コージェネレーションシステム
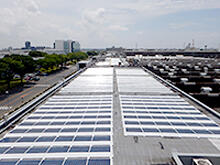
藤沢工場太陽光発電パネル
廃棄物の削減 - 最終埋立て処分量推移
目標
埋立処分量(トン)/廃棄物総発生量(トン)=1%以内
2014年度実績
埋立処分量(トン)/廃棄物総発生量(トン)=0%
※最終埋立処分量:0 トン、廃棄物総発生量:7.71千トン
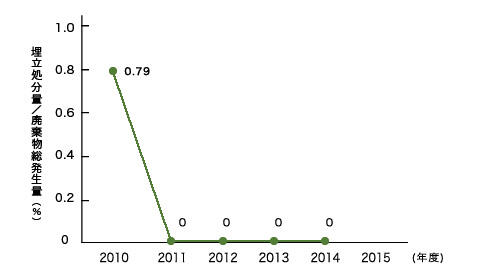
分別管理の徹底や様々な廃棄物削減のための取り組みにより、埋立処分量0トンを維持することができました。
廃棄物削減のための主な取り組み
- 新買取先開拓による有価対象品目拡大
- 分別回収の徹底と解体による再資源化推進
- 廃棄物総量削減と副産物削減活動推進
- プラスチック製品のマテリアルリサイクル化推進
- 廃油分別による再生利用拡大
- 発泡スチロール付着粘土のリサイクル化促進
- 仕切り材として使われる木くずを返却し、排出を削減
- ヘルメットやライトキャップの有価物化推進
- 小型充電式電池の資源化
- 循環水槽の薬品変更による塗料かす削減
- 鍛造工程等で発生する鉄粉を鋼材原料としてリサイクル化 等
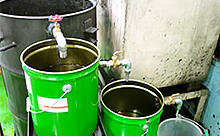
廃油分離装置
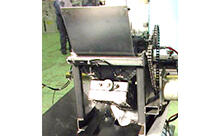
鉄、紙分離装置
水資源の有効活用
地下水を浄化処理して工場内の生活用水に使用するとともに、節水や最終水処理工程での再利用化を進め、水資源の有効活用を図っています。
2014年度実績
水使用量:211万m3
水使用量の多い藤沢工場では、電着塗装工程における洗浄水の繰り返し使用や生活排水の処理水をトイレ用として再利用する等の節水活動を行っていますが、2014年度は生産量増加に伴い、水使用量が2013年度比約4%増となりました。
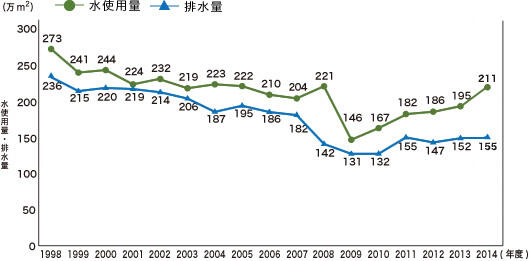
揮発性有機化合物(VOC※)低減(藤沢工場)
※VOC:Volatile Organic Compounds(揮発性有機化合物)の略で有機溶剤が主となります。
目標
VOC発生率:19.2 g/m²以下
2014年度実績
VOC発生率:18.3 g/m²
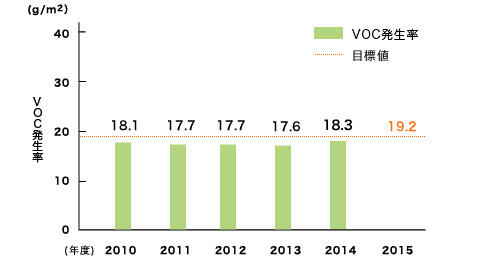
環境関連教育
環境関連教育として、環境一般教育や関連法令、ISO内部監査員に対する諸研修を行っています。
2014年度実績
項目 | 2014年度実績 | |
---|---|---|
環境一般教育 | 新入社員向け | 565人 |
3R推進月間時 | ||
省エネ月間時 | ||
環境法令教育 | 199人 | |
ISO内部監査員教育 | 新人研修 | 229人 |
養成研修 | ||
レベルアップ研修 | ||
勉強会 |
事業活動と環境負荷
いすゞは製品のライフサイクル(開発~調達~製造~物流~製品稼働~廃棄)を通じて環境負荷の低減を行うため、環境負荷の高いプロセスを中心に、その影響を把握しています。
2014年度実績
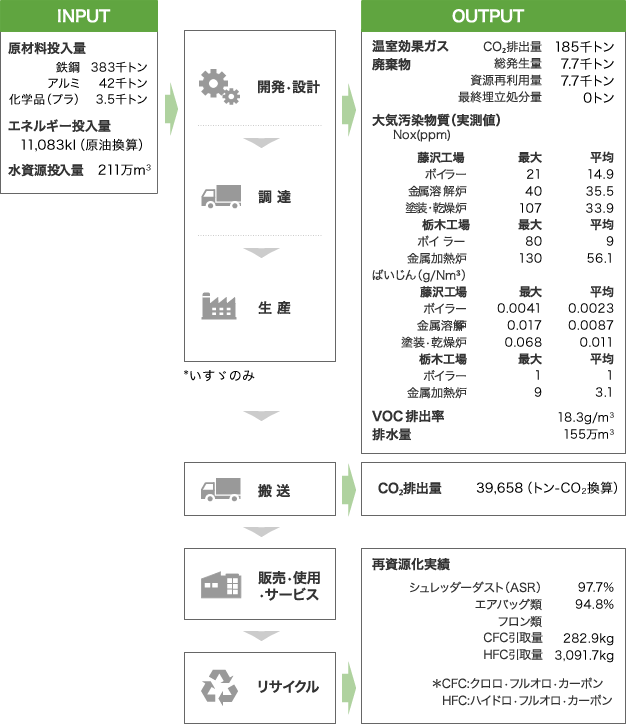